When choosing the right display for an industrial application, we need to consider a number of key factors. Firstly, the screen size and resolution have a direct impact on the clarity of the display; secondly, the temperature of the working environment and the mounting method (e.g. panel, rack or open frame) must match the actual requirements. In addition, the choice of touch screen (resistive, capacitive or PCAP) and various safety certifications (e.g. UL, NEMA, IP, DNV GL, etc.) are also important indicators to ensure durable and stable operation.
In conclusion, this article will provide you with a detailed analysis of how to select a reliable and efficient industrial monitor based on different application scenarios and budgets.

Characteristics of Monitors
When selecting an industrial display, understanding its key technical specifications can help match the needs of various applications. Here are a few core factors that determine display performance and durability:
Display screen size and resolution
Industrial displays are available in a wide range of sizes, typically ranging from 7 inches to 23.8 inches. Smaller displays are suitable for compact spaces, while larger sizes are suitable for information-intensive applications such as production monitoring or data visualisation. In terms of resolution, the higher the resolution, the more detailed the display. Common options include 1024 x 768 (XGA), 1280 x 1024 (SXGA), 1920 x 1080 (Full HD), etc. The appropriate resolution should be selected according to the application requirements.
Brightness and Contrast Ratio of the Monitor
Brightness (in nits) determines the visibility of the monitor in different light environments. Standard industrial displays are usually between 300-1000 nits, while high brightness displays for outdoor or bright light environments can reach 1500-2500 nits. in addition, the higher the contrast ratio, the clearer the image, especially in applications that need to display data accurately.
Display Viewing Angle
Viewing angle determines the clarity of the screen when viewed from different angles; IPS (In-Plane Switching) panels offer an ultra-wide 178° viewing angle, ideal for industrial scenarios where multiple people need to view the screen at the same time, while TN (Twisted Nematic) panels are more advantageous in applications with high refresh rate requirements.
Display Corrosion Resistance and Durability
Industrial environments often involve dust, moisture, chemicals or extreme temperatures, so displays should be protected accordingly. For example, IP65 protection is effective against dust and water, while corrosion-resistant screens with special coatings are suitable for medical, food processing or marine environments. In addition, some industrial monitors are also shock and vibration resistant to ensure stable operation in harsh conditions.
Taking all these factors into account, choosing the right industrial monitor not only improves efficiency, but also extends the life of the equipment and reduces maintenance costs. Next, we will explore different installation methods and their applicable scenarios.
Installation and Application Scenarios of Displays
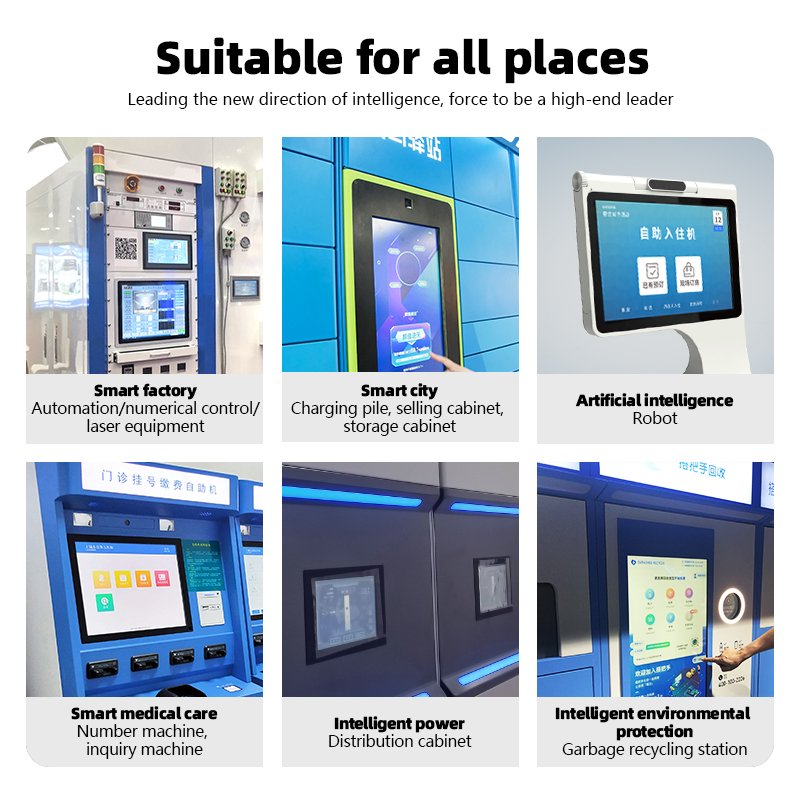
The mounting method of industrial monitors directly affects their application environment and operation convenience. Different mounting methods can meet the needs of different application scenarios. the following are several common mounting methods and their characteristics:
- Panel Mount
Panel Mount is an embedded mounting method for cabinets, consoles or industrial equipment panels. When mounted, the front panel of the monitor is embedded in the equipment and secured by screws or clips. This method provides a high level of protection (e.g. IP65 against dust and water) and is suitable for industrial automation, HMI (Human Machine Interface) and medical equipment scenarios. - Rack Mount
Rack Mount is designed for standard 19’ server cabinets, typically used in data centres, industrial control rooms or broadcasting. The displays come with standardised fixing holes and can be easily mounted in 1U or 2U racks. This is ideal for scenarios where multiple devices need to be centrally managed, such as network monitoring, server management and remote operations. - Flush Mount
Seamless flush mounting is similar to panel mounting, but focuses more on seamless integration with the device enclosure so that the monitor blends in with the console or wall. This approach is not only aesthetically pleasing, but also reduces dust accumulation and is suitable for environments with high cleanliness requirements, such as medical, food processing, and laboratory environments. - Open Frame
Open Frame displays (Open Frame) do not have an enclosure and usually only include a screen and a fixed bracket, making it easy to integrate into systems such as self-service terminals, ticket vending machines, ATMs, industrial control equipment, and so on. Its flexible design is suitable for OEM (Original Equipment Manufacturer) and customisation projects. 5. - Arm Mount
Arm Mount allows users to freely adjust the height, angle and position of the display, which is suitable for working environments that require flexible manoeuvring, such as production lines, medical diagnostic equipment and industrial machinery consoles. Some high-end cantilever mounts also feature pneumatic adjustment for one-handed operation. - Wall Mounts
Wall Mount uses a VESA standard bracket to secure the monitor to the wall, saving desktop space. This method is suitable for factory production lines, monitoring centres, intelligent warehouses and other scenarios that require remote monitoring or fixed displays. - Desktop Stand
Desktop stand mounting is suitable for office, test and laboratory environments, where users can adjust the angle and height as needed. Some industrial monitors are equipped with a sturdy metal base to ensure stability and prevent vibration and movement.
Different mounting methods are suitable for different application scenarios. Choosing the right mounting method not only enhances the safety and durability of the equipment, but also optimises the operating experience and improves productivity.
Touch screen types for monitors
Common touch screen types for industrial monitors include resistive, capacitive and infrared touch screens, each with different characteristics:
Resistive touch screen:
Relying on pressure sensing, it supports glove and stylus operation and is suitable for dusty and humid environments, but with low light transmission and general wear resistance.
Capacitive touch screen:
Through the electric field induction, support for multi-touch, sensitive operation, good display, but does not support the operation of ordinary gloves, affected by water and electromagnetic interference.
Infrared touch screen:
Using infrared beam detection, can use any object touch control, suitable for large screen applications, but affected by external light, need to dust and dirt.
How to choose?
Harsh environment (high humidity, wearing gloves): choose resistive or infrared screen.
High precision, multi-touch: choose capacitive screen.
Large size display (32 inches or more): choose infrared screen.
Connectors for Industrial Displays
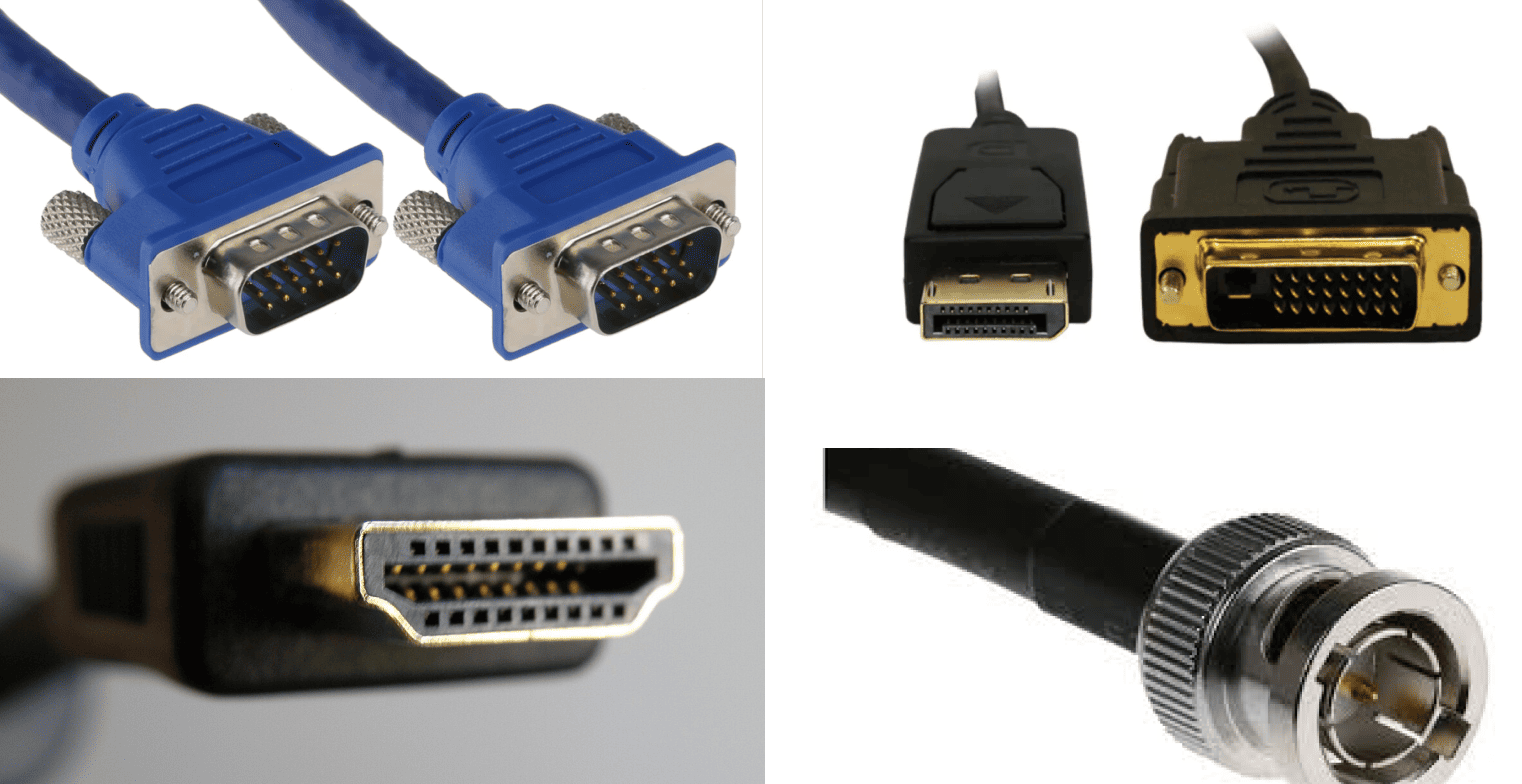
The connection interface of an industrial monitor determines its compatibility with other devices and display effect. Different ports are suitable for different application requirements, the following are common interface types:
- VGA (Video Graphics Array):
Traditional analogue interface, supports up to 1920 x 1080 (1080p) resolution, suitable for older equipment or basic display needs. - DVI (Digital Video Interface):
Clearer picture quality than VGA, supports higher resolution (up to 2560 x 1600), commonly used in industrial PCs and older embedded systems. - HDMI (High Definition Multimedia Interface):
Supports high-definition video and audio transmission and is widely used in modern industrial displays, offering 4K resolution for remote monitoring or high-definition applications. - DisplayPort (DP):
Faster than HDMI, supports higher resolution and multiple screen outputs for high performance industrial computing and data visualisation. - LVDS (Low Voltage Differential Signalling):
Mostly used in embedded systems, suitable for short-distance high-speed data transmission between the motherboard and the display, energy saving and strong anti-interference ability。 - BNC (video coaxial interface):
Commonly used in security monitoring systems, providing high stability video transmission, strong anti-interference ability, and suitable for professional monitoring equipment.
How to choose?
Older equipment or basic applications → VGA/DVI.
High-definition display needs → Select HDMI/DisplayPort.
Embedded device or motherboard direct connection → select LVDS.
Security monitoring applications → select BNC.
Screen Technology Selection for Industrial Displays
Different display technologies determine the brightness, colour performance, energy consumption and service life of an industrial monitor. Common screen technologies include:
- LCD (Liquid Crystal Display):Currently the most common industrial display technology, using CCFL or LED backlighting, stable colour and low power consumption, suitable for most industrial environments.
- LED (Light Emitting Diode):Essentially a type of LCD screen, but using LEDs as the backlight, it is brighter and consumes less energy than traditional LCDs, and is suitable for outdoor or bright light environments.
- OLED (Organic Light Emitting Diode):No need for backlight, self-luminous technology provides higher contrast and wider viewing angle, but easy to aging, higher price, not suitable for long-term display of static content of industrial applications.
- Plasma screens (Plasma):With high brightness and wide viewing angle, but high energy consumption, easy to burn the screen, has been gradually replaced by LCD and LED, less used in industrial applications.
- How to choose?
- Indoor standard application → choose LCD (CCFL/LED backlight).
- Outdoor high brightness environment → choose LED backlight LCD.
- High contrast, high colour demand → OLED (but not suitable for long time displaying static images).
Protection Standards for Industrial Displays
Industrial displays are required to meet a variety of protection standards to ensure stable operation in harsh environments. Choosing the right protection standard can increase the reliability and lifetime of industrial displays. Common standards include:
- IP (Ingress Protection) ratings:Dust and waterproof standards, such as IP65 (dust and water spray), IP67 (can be short-term water immersion), for wet, dusty environments.
- IK (Impact Resistance Rating):Evaluates the impact resistance of a screen, e.g. IK10 is suitable for high intensity impact requirements such as public kiosks.
- ATEX (explosion proof certification):Suitable for flammable and explosive environments, such as the petroleum and chemical industries, to ensure safe operation of equipment in hazardous areas.
- MIL-STD-810G/F (Military Standard):Ensure the equipment can withstand extreme temperature, vibration, shock and other harsh working conditions, applicable to military and heavy industrial environments.
How to choose?
Wet and dusty environment → Choose IP65 or above.
Susceptible to external impact → choose IK10.
Explosion-proof requirements → Select ATEX certification.
Extreme environments (high temperature, vibration) → MIL-STD-810G/F.
Environmental Adaptability of Industrial Displays
Industrial displays need to operate stably in various extreme environments, mainly considering the following factors:
- Operating temperature: the standard range is generally -10°C to 60°C. For extreme environments, high and low temperature resistant models should be selected, such as -40°C to 85°C, which are suitable for outdoor, cold chain or high temperature workshops.
- Environmental durability: Vibration, shock and corrosion resistance for high mechanical stress environments such as smart manufacturing and traffic control.
- Optical Bonding: Seamlessly bond the display panel to the glass layer to improve brightness, anti-reflective properties and impact resistance, suitable for direct sunlight environments such as automotive and outdoor displays.
- How to choose?
- High and low temperature environments → Choose a wide temperature screen (-40°C to 85°C).
- Shock and vibration scenarios → Choose impact and corrosion resistant design.
- Outdoor bright light applications → Choose optical lamination technology to reduce reflection and improve clarity.
Reasonable selection of environmental durability configurations to ensure long-term stable operation of the monitor in different industrial environments.
Choosing the right industrial monitor to enhance the efficiency of industrial applications
When choosing an industrial monitor, factors such as screen size, resolution, mounting method, touch technology, connection interface, display technology, protection standards and environmental adaptability are all critical. Different application scenarios require different configurations to ensure the stable operation of the equipment in harsh environments and to provide the best display effect and operating experience.
Uinda provides high-performance industrial displays to meet various industrial needs

As a professional industrial monitor manufacturer, Uinda provides 7‘’ to 23.8‘’ industrial touch monitors with IP65 dustproof and waterproof, wide-temperature operation (-10°C~60°C), high-brightness optical lamination, and support for VESA, panel, and rack mounting, which are suitable for intelligent manufacturing, transportation, automation control and other fields. In addition, Uidna also provides customisation services to adjust the interface, touch technology and protection level according to your project requirements.
👉 Contact us today for professional industrial display solutions!